3D-printed Affordable Community in Austin, Texas
Icon's Vision For 3D-Printed Homes In Austin, Texas
In the heart of Central Texas, the hill country, a revolutionary approach to housing is taking shape, spearheaded by the visionary team at ICON. This innovative company is on the forefront of utilizing cutting-edge 3D printing technology to construct homes in Austin, Texas. ICON's vision extends far beyond merely building houses; it aims to fundamentally transform how we think about construction, community, and sustainability in the 21st century.
At its core, ICON's initiative seeks to address several critical challenges facing urban development today: affordable housing shortages, environmental sustainability, and the efficiency of construction practices. By harnessing the power of large-scale 3D printing technology, ICON is capable of producing resilient and aesthetically pleasing homes at a fraction of the time and cost associated with traditional construction methods. This groundbreaking approach not only opens doors for more affordable housing options but also significantly reduces waste and carbon footprint.
Austin, Texas serves as an ideal incubator for this ambitious project. The city's vibrant culture of innovation and its growing demand for sustainable living solutions align perfectly with ICON's mission. As these 3D-printed communities begin to take shape in Austin's landscape, they promise not just a new form of housing but a new way of living—where design innovation meets practicality in addressing some of today’s most pressing societal issues.
ICON’s venture into 3D-printed homes in Austin is more than an experiment; it's a bold step towards reimagining the future of urban habitation through the lens of technology and social responsibility.
Are 3D - Printed Homes more Eco-friendly and Affordable?
Yes, 3D-printed homes are considered more eco-friendly and affordable compared to traditional construction methods.
Eco-friendliness: 3D-printed homes produce less waste during the construction process because a precise amount of materials is used. They require less labor and can function on renewable energy sources. Also, the process can often use recycled materials, reducing the need for new resources.
Affordability: 3D-printed homes have the potential to be significantly cheaper than traditionally built homes. The cost of machines used for construction is decreasing and the speed of construction is faster, resulting in lower labor costs. The ability to print continuously can also cut down the construction time by weeks or even months. Additionally, the ability to customize the design of the house without significantly affecting the cost makes it a cost-effective construction alternative.
CAN YOU 3D PRINT A HOUSE ?
3D printing a house involves the following steps:
1. Designing: The first step is to design the house using a CAD (Computer Aided Design) software. The design has to be meticulous with every minor detail, including doors, windows, electrical outlets, plumbing, among others. The design is then converted into a 3D model.
2. Slicing: The 3D model is divided into thousands of horizontal layers or slices using specialized software. This slicing process turns the digital 3D model into a file readable by the 3D printer, and it instructs the printer about the amount of material to be deposited layer by layer.
3. Material Preparation: It is necessary to prepare the building mix or “ink” for the 3D printer. The mix is often a type of concrete or proprietary blended material that is suitable for 3D printing. Some companies use a mixture that includes recycled materials.
4. Printing: Using a 3D printer, the design is printed layer by layer. The printer follows the preprogrammed path set by the sliced files to deposit the print material.
5. Assembly: Some parts of the building may not be 3D printed such as the roof, windows, and doors. Once the walls have been printed, these other parts are installed using traditional construction methods.
6. Finishing: This involves the fitting of utilities like electricity, plumbing, painting, and the installation of fixtures based on one's preferences.
It's important to note that while the technology significantly speeds up the building process and can save on costs, it’s still quite new and is not yet widely used. It's not suitable for every type of building and the amount of manual work required after the main structure has been printed can vary significantly.
WHAT ARE 3D PRINTED HOMES MADE OF?
3D-printed homes are generally made of a concrete mixture, which is extruded through a nozzle in layers to build the walls and structures. The concrete mixtures used in 3D printing are usually enhanced with additives to improve their performance in terms of flowability, buildability, and open time.
The concrete used in 3D printing needs to be able to support the weight of each layer and dry quickly enough to hold its shape once extruded.
Some companies also experiment with proprietary mixes, some of which include materials like recycled plastic or industrial waste byproducts. Remember that typically only the primary structure of the home - mainly the walls - is 3D printed. Components like the roof, windows, doors and installations are usually finished using traditional construction techniques.
Remodeling homes with 3D printer technology?
Using 3D printing technology for remodeling homes is a growing trend in the construction industry. With 3D printers, homeowners can create custom features, fixtures, and furnishings for their homes. Here's how 3D printer technology can be used in remodeling:
1. Customization: 3D printing allows for great design flexibility. You can print unique and personalized elements such as doorknobs, cabinet handles, light fixtures, floor tiles, and more.
2. Replacement parts: If a part of a fixture or a piece of furniture is missing or broken, creating the replacement part is easy with 3D printing. Instead of searching for the part in stores, you can simply 3D print it.
3. Cost savings: In some cases, 3D printing parts or fixtures can be more cost-effective than buying them. You can design and create your own items rather than purchasing them at a higher price.
4. Time-saving: 3D printing can significantly reduce the time needed for production and delivery of certain parts or furniture.
5. Restoration: In classic homes, it could be hard to find parts that are not produced anymore. With 3D printing, you can recreate these parts in an easier and more efficient way.
However, it's crucial to note that while 3D printing can be beneficial, it may not always be the best solution. The quality of 3D printed items can vary, and they may not always meet local building codes or standards. For larger scale remodels involving structural changes, traditional construction methods are still mostly used.
Pros and Cons 3D-Printed Homes: Sustainability And Efficiency
The advent of ICON's 3D-printed homes in Central Texas, specifically within the pioneering endeavors of ICON in Austin, marks a significant stride towards redefining residential construction through sustainability and efficiency. This innovative approach to building homes not only streamlines the construction process but also introduces a new era of environmental consciousness and resource management in the housing sector.
Pros:
1. Resource Efficiency: 3D printing uses only the amount of material necessary for the construction process, reducing waste.
2. Speed: 3D-printed homes can be constructed in a matter of days or weeks, much faster than traditional construction methods.
3. Sustainability: Some 3D printing techniques use eco-friendly materials such as recycled plastics or locally-sourced soils. This can help to reduce the home's carbon footprint.
4. Cost: 3D-printed homes are usually less expensive than traditionally-built homes due to less labor and material necessary.
5. Power Efficiency: The 3D printers used in construction are typically electric and, as such, could be powered by renewable energy.
Cons:
1. Limited Designs: Although 3D printing allows for some design flexibility, there are limitations to the complexity and size of buildings that can be constructed with current technology.
2. Durability: The long-term durability of 3D printed homes is still somewhat unknown, although tests on short-term durability have been positive.
3. Regulations: Many areas have strict building codes and regulations that do not account for 3D-printed constructions. This can make obtaining the necessary permissions more difficult.
4. Quality: The quality of a 3D-printed home can depend heavily on the technology and materials used. If done poorly, a 3D-printed home can have structural weaknesses.
5. Jobs: The rise in 3D-printed homes could potentially lead to job losses in the traditional construction industry.
As the technology progresses, it's likely that many of these cons will be resolved or mitigated, making 3D-printed homes an even more appealing option for sustainable and efficient housing.
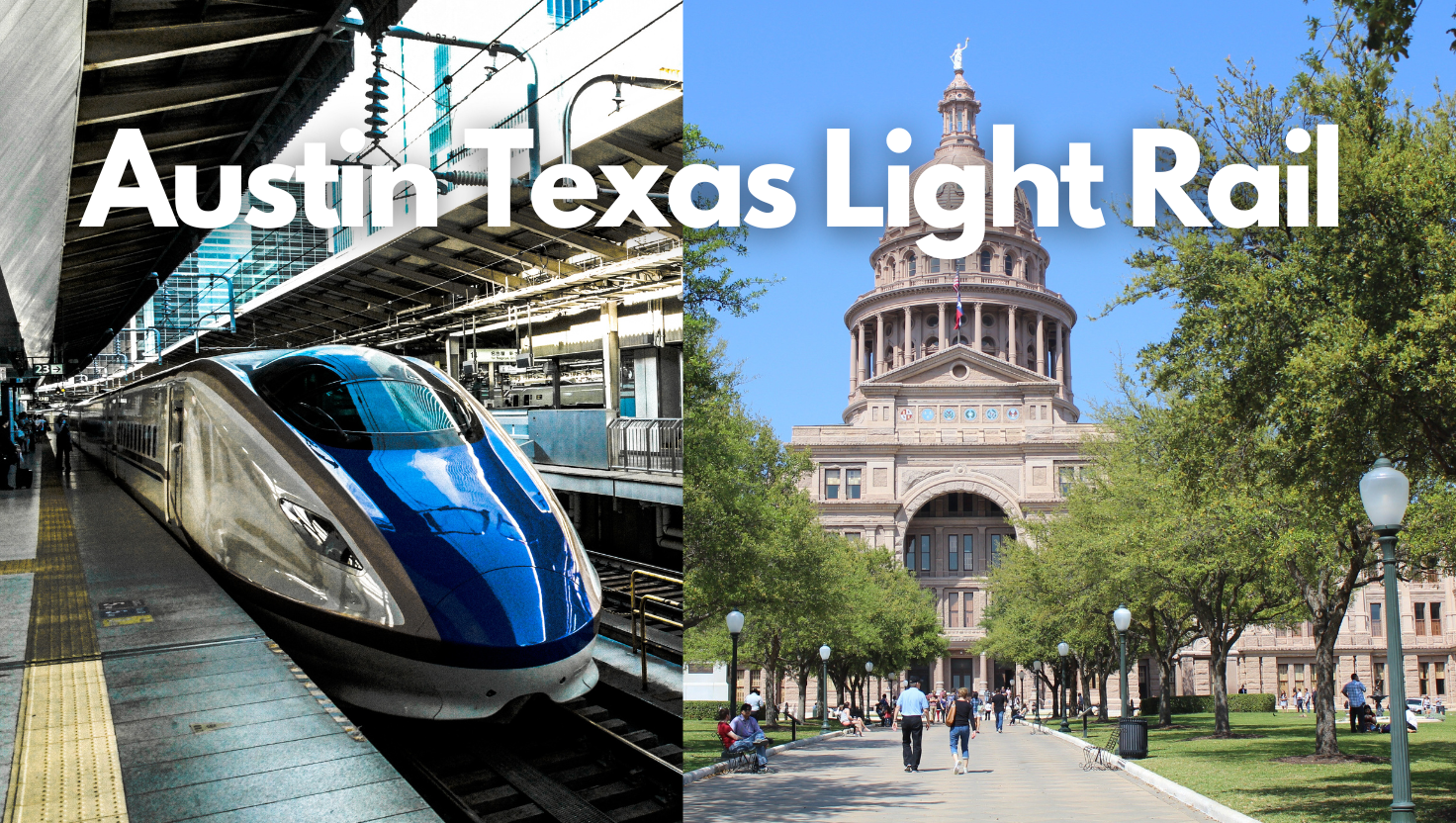
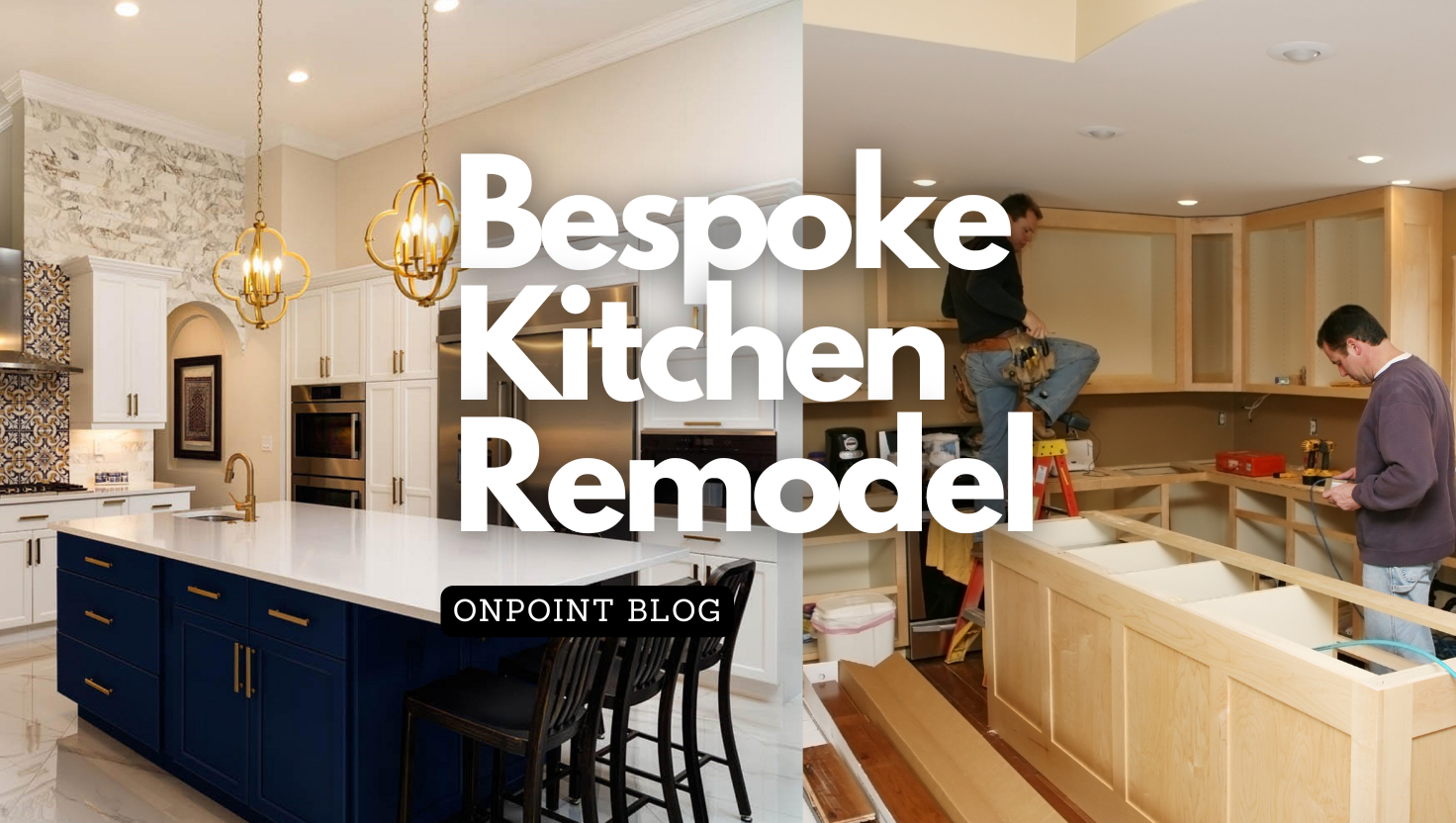
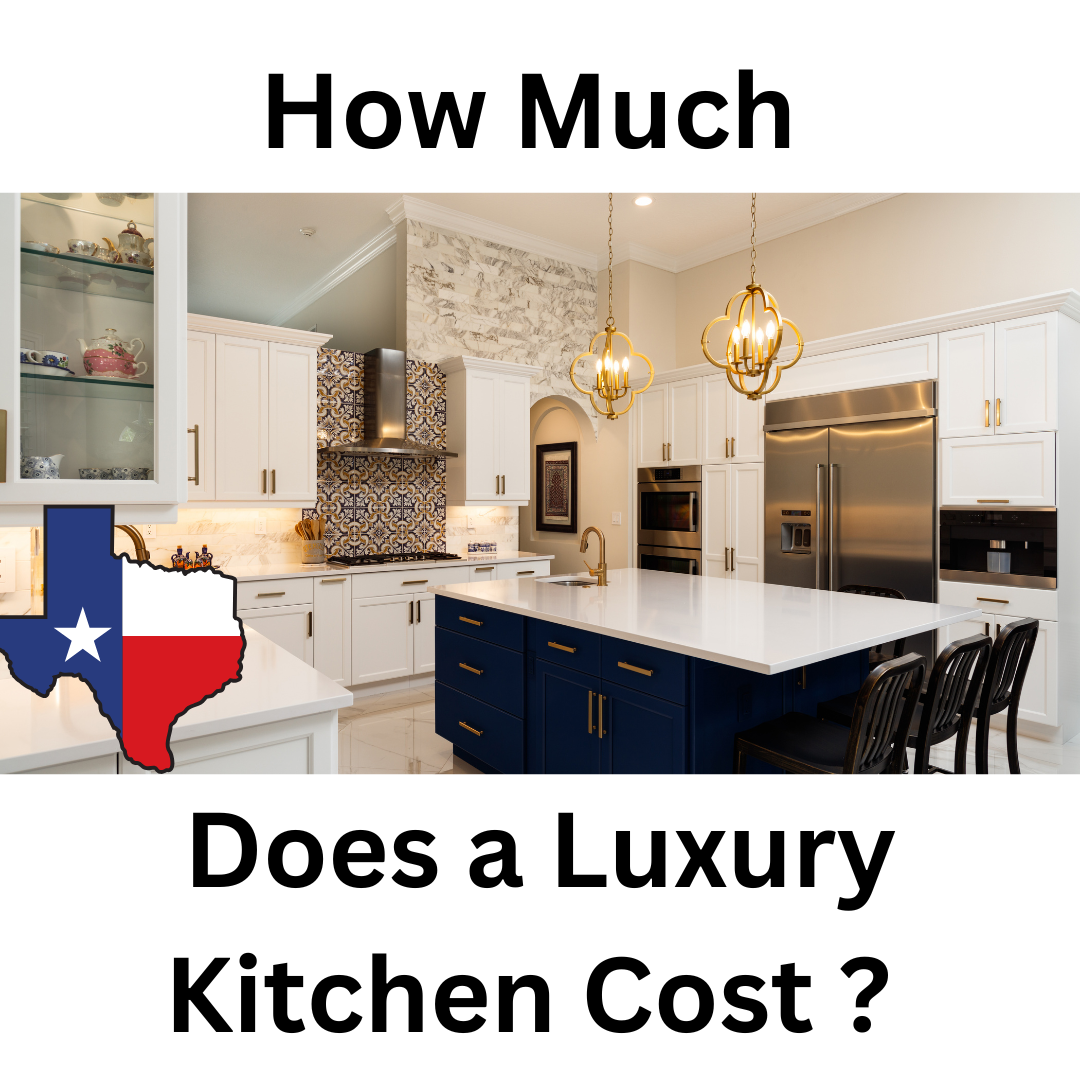
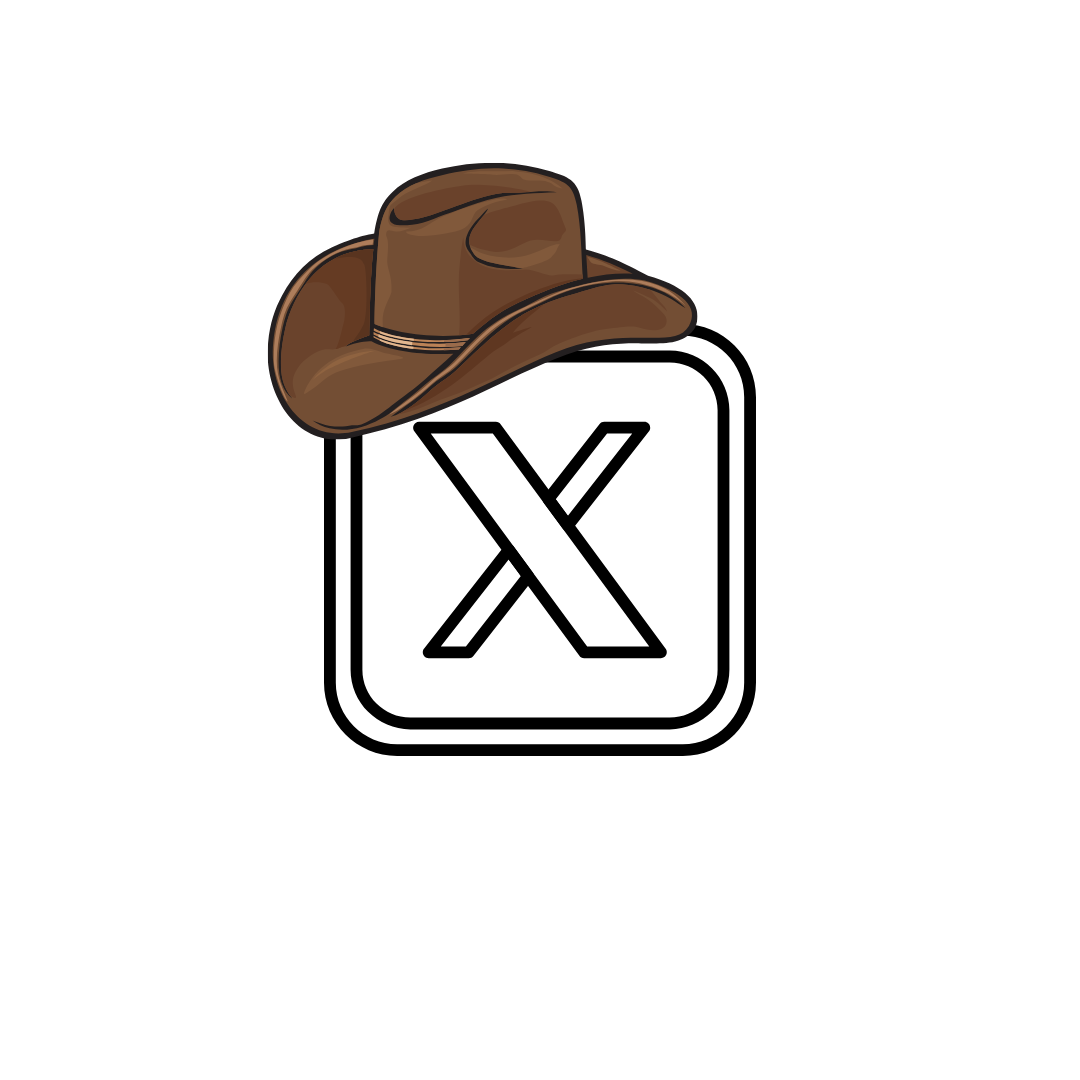
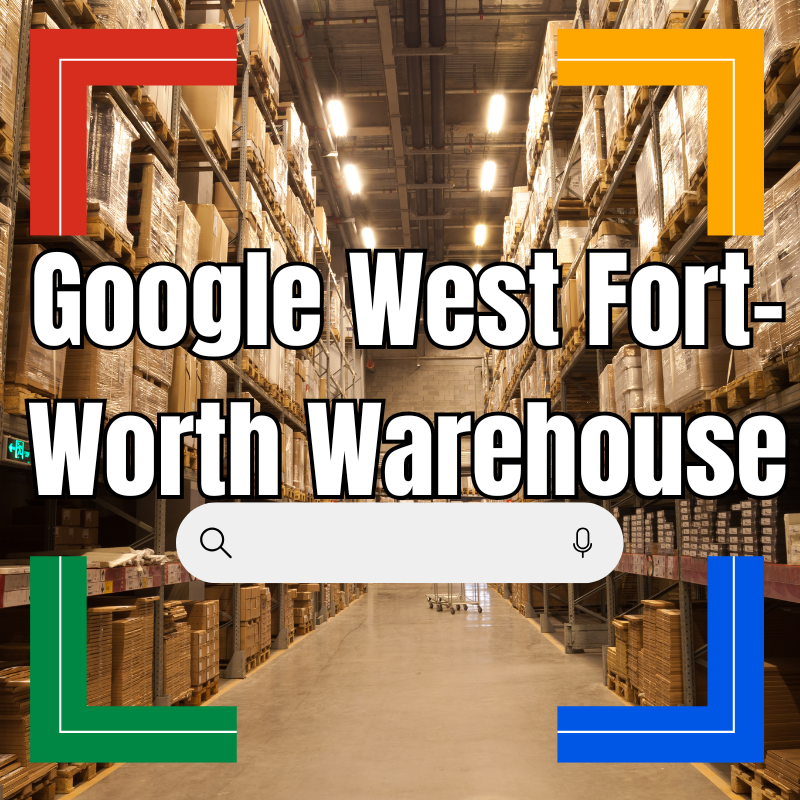
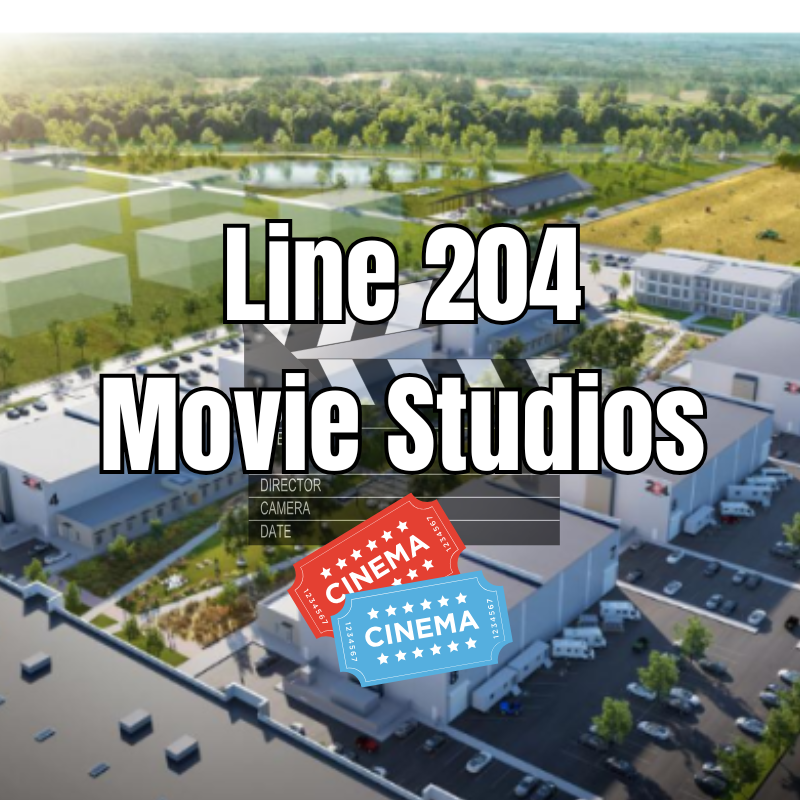
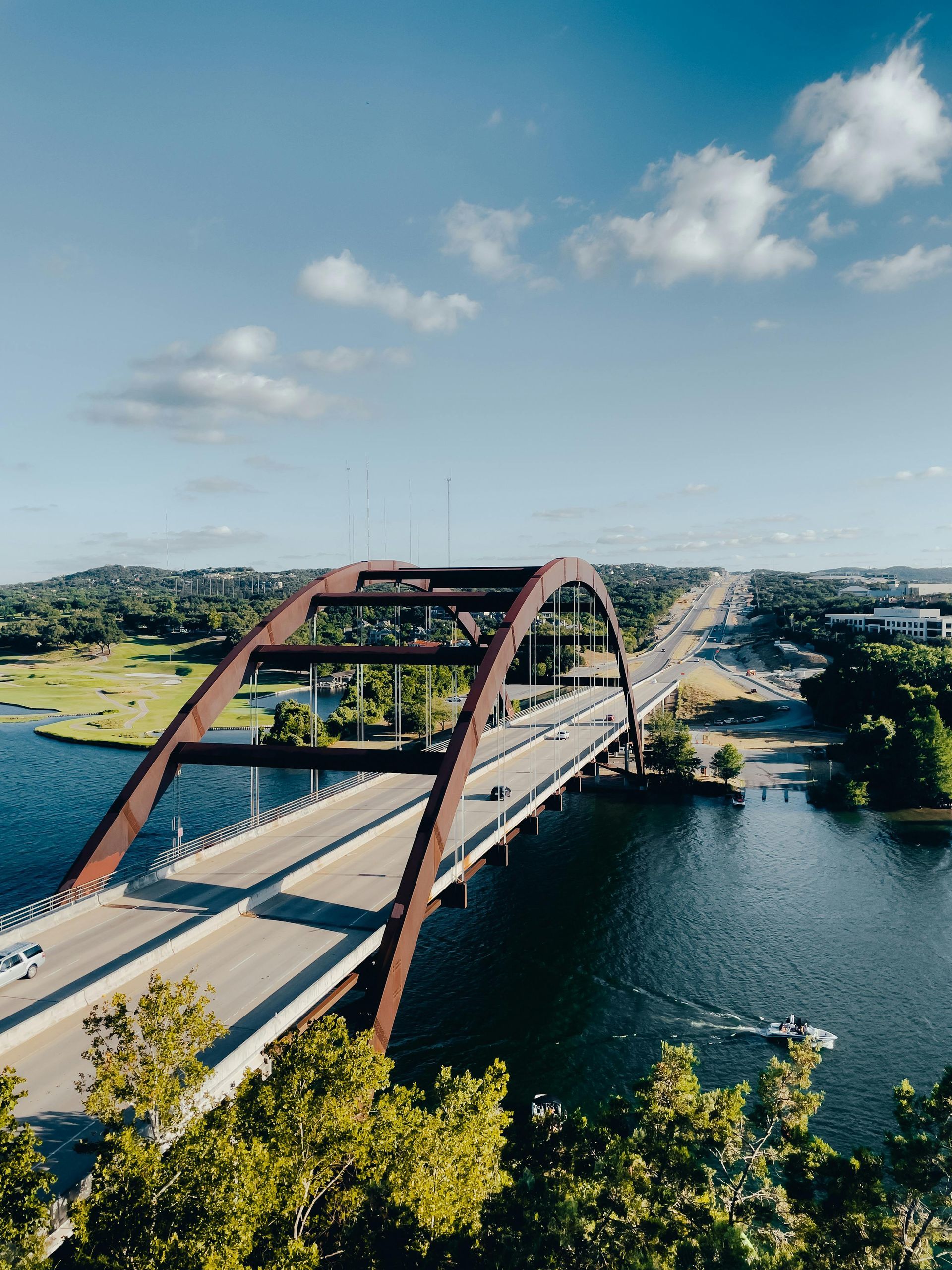
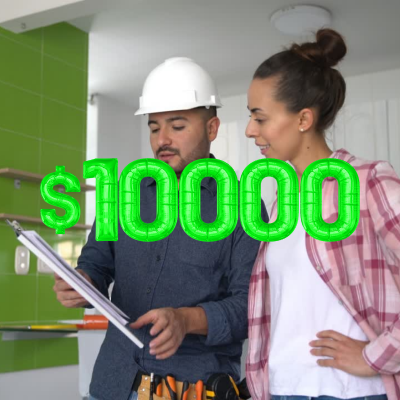
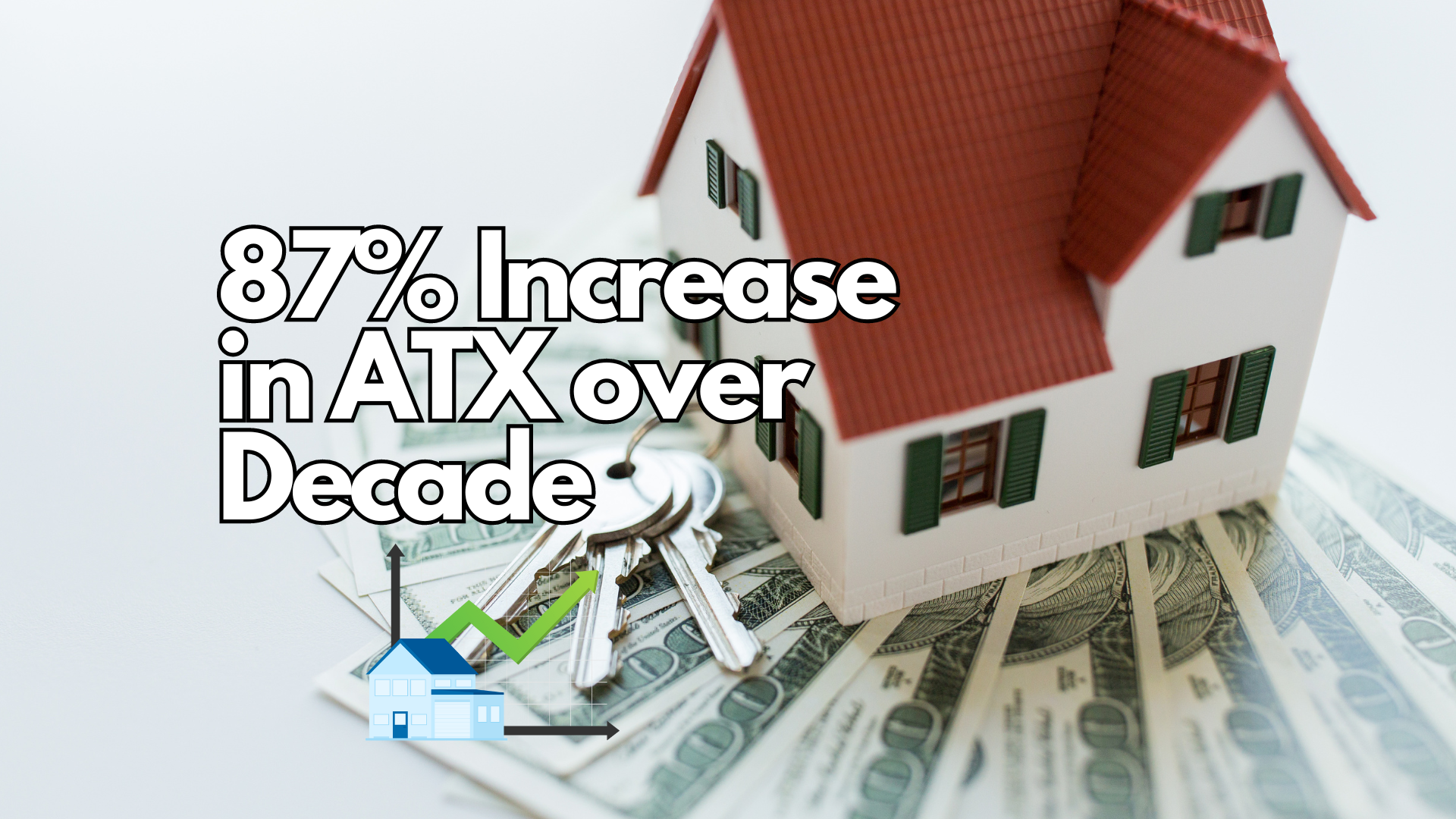
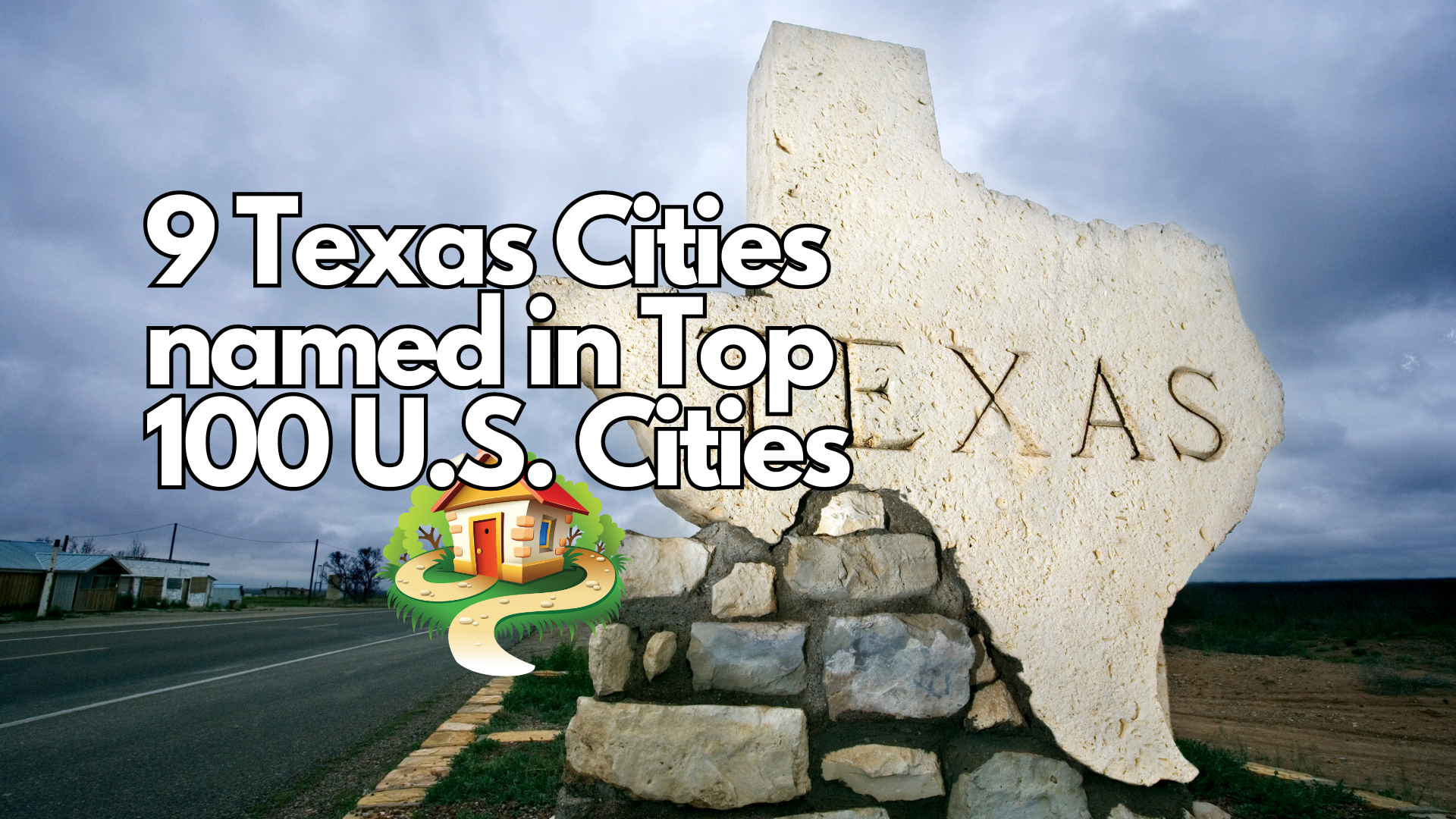